Types of Commercial Roofing
If you own a commercial property, the roofing materials are vital in determining the building’s longevity and sustainability. Roofing contractors can recommend the best materials that will minimize repair costs in the future.
There are two primary types of commercial roofs – single-ply membranes and thermoplastics. Both provide insulation and resistance to punctures, bacteria, oils, and chemicals.
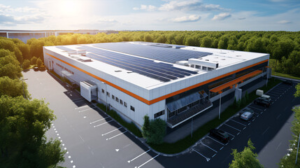
Flat roofs are the most common type of roof on commercial buildings. They offer several perks, including storing more material, reducing energy costs and creating more space for other amenities. In addition, they are easy to access and require less maintenance than sloped roofs. However, they aren’t suited for all environments and climates. You should consult with a professional roofing contractor to determine what the best flat roofing system is for your property.
There are many different types of commercial roofs, but the most popular is a single-ply membrane made from polyvinyl chloride (PVC). These types of flat roofing systems are highly durable and can withstand weather extremes. They also feature strong seams that can prevent leaks. However, they are prone to punctures and aren’t as flexible in hot temperatures as other roofing materials.
Built-up roofs (BUR) are another popular option for commercial roofing. These roofs have been used in the U.S. for decades and are sometimes referred to as tar and gravel roofs. They consist of alternating layers of asphalt and reinforcement fabrics. The number of plies in the roof signifies how thick it is. BUR roofs are fire-resistant and require little maintenance, but they do not hold up as well against extreme heat.
Commercial roofing contractors can use a variety of materials for flat roofs, including rubber, PVC, and thermoplastic polyolefin (TPO). These systems are highly durable and can withstand harsh chemicals. They are also aesthetically appealing and can provide a uniform appearance for the building’s exterior. They are also very cost-effective.
Flat roofs are ideal for areas with warm weather, but they can be used anywhere. They do not perform as well in cold areas because they cannot accommodate ice, snow, and freezing temperatures. Additionally, they are not good for areas with heavy rainfall. In these cases, the water may pool and cause damage to the roof surface or interior walls.
Flat roofs also have a lower life expectancy than other types of roofs, but they can be extended with proper maintenance. You should check your flat roof for leaks, wear and tear, and any other problems on a regular basis. If you have a flat roof, you should also consider installing a siphonic drainage system to prevent the buildup of water and debris. You can also add insulation to your roof, which will help to prevent water from seeping into the structure of the building.
The roof of a commercial building has a significant impact on its overall function and appearance. As such, it’s important to understand the different types of roofing systems available so you can make an informed decision about what is best for your business. Low-slope roofs, also known as flat or zero-slope roofs, are a common option for commercial buildings because of their cost-efficiency and versatility. They require fewer materials and less labor during installation than steep-slope roofs, which helps keep costs down for the project. Low-slope roofs also offer a variety of advantages over other types of roofs, including their versatility in design and their ability to accommodate HVAC and solar panels.
The term “flat” is misleading because it doesn’t necessarily mean a completely flat surface. Most low-slope roofs have a very slight pitch – or slope – to help with water drainage. Because of this, it’s important to choose the correct roof system for a low-slope roof to avoid leakage or structural damage.
Unlike steep-slope roofs, which can accommodate a wide range of roofing materials, low-slope roofs are most commonly covered with membrane roof systems. These are typically single-ply or multi-ply membranes made of PVC, EPDM, or TPO. These are usually white and reflect sunlight to help keep the building below cooler, which can save on energy costs in the long run.
Although they are cheaper and easier to install than steep-slope roofs, low-slope roofs have their own unique challenges. The lack of a steep slope can cause debris to build up on the roof, and it can be difficult to access areas for maintenance and repairs without a ladder. In addition, the lack of a slope can also result in water accumulation on the roof, which can lead to leaks and other problems.
A qualified commercial estimator can help you select the right low-slope roof for your project. They can provide an accurate cost estimate and help coordinate the work to ensure it’s completed on time and within budget. They can also recommend the right roof system for your project based on the type of building and its purpose, as well as the climate where it’s located.
Single-ply membranes are popular in commercial roofing because of their low cost and durability. They also take less time to install than built-up systems because they are rolled out in large sheets and easily fastened together. Additionally, they are available in a variety of colors and can be adapted to reflect certain energy needs. For example, PVC and TPO are a popular choice for “cool roofs,” helping keep cooling costs down in hot climates.
The most common single-ply membranes used in commercial roofing are thermoplastic polyolefin (TPO) and ethylene propylene diene monomer (EPDM). These roof membranes offer many benefits. TPO is highly durable and has good resistance to UV rays. EPDM has excellent elasticity and can expand and contract to accommodate temperature changes. In addition, it is odorless and easy to work with, making it a great choice for medical facilities or multi-family dwellings.
Both types of single-ply membranes have their pros and cons, so deciding which one is right for you will depend on your specific requirements, including cost, climate, energy efficiency, and the roof’s location and design. For example, a TPO roof with white reflective surface can help reduce energy costs in warmer climates. However, it is important to remember that a single-ply membrane does not have a built-in redundancy and any puncture or faulty seam will allow water to seep into the roofing substructure, leading to structural damage and potential leaks.
Another disadvantage of single-ply membranes is that they do not have the same durability and lifespan as more traditional, multi-ply bituminous membranes. If you are considering a single-ply membrane, talk to a professional about the type of insulation that is most appropriate for your building.
There are two ways that single-ply membranes can be installed: ballasted or mechanically fastened. In a ballasted system, the roof membrane is secured to the roof deck with a layer of ballast, typically river-washed gravel or concrete pavers. The resulting surface is relatively flat and can be easily walked on for maintenance and inspections. A mechanically fastened system, on the other hand, uses lines of fasteners to attach the sheets of membrane to each other and the roof deck. In some cases, batten strips are added along the fastener lines for increased security.
Metal roofs are growing in popularity due to their durability, environmental sustainability, variant styles, and flexibility. They can withstand regular wear and tear, harsh environments, and exhaust and pollutants, making them a solid choice for commercial buildings that require robust protection against the elements. In addition, they can be formed into unique textures, shapes, and colors that fit with the overall aesthetic of the facility, adding to the design flexibility.
Unlike traditional shingles, metal roofs are non-combustible, meaning that they don’t attract lightning and can’t corrode in the event of fire. They also shed snow and water easily, protecting the rest of the building’s exterior. And because they can be covered with reflective coatings, they help reduce energy costs by keeping the interior of the building cooler.
A metal roof can last for up to 60 years and requires minimal maintenance. It is also highly durable and able to resist high winds and hail storms. It can withstand up to 140 miles per hour, making it an excellent option for hurricane-prone areas. Furthermore, it can withstand frequent rainstorms and heavy snowfall.
There are several different types of metal roofing, including corrugated, standing seam, and single-ply. Corrugated metal is a popular choice for commercial roofing due to its low initial cost and long lifespan. Standing seam metal is another popular option, as it provides superior durability and a sleek appearance. Single-ply metal is a great choice for commercial roofing because it offers superior leak resistance and withstands heavy rainfall.
When installing a metal roof, it is important to hire a reputable contractor specializing in this type of work. A knowledgeable and experienced contractor can ensure the quality of installation and provide tips for ongoing maintenance. In addition, a reputable company will offer a warranty on their workmanship.
As more facility executives place a greater emphasis on lifecycle costs and sustainable materials, metal roofs are increasingly becoming the roofing of choice for many new commercial facilities. This is especially true for buildings that are undergoing renovations or retrofits, as metal roofs can often be placed directly over existing asphalt shingles and other roofing systems without the need for a costly tear-off.